The Essential Role of Vacuum Stations in Modern Industry
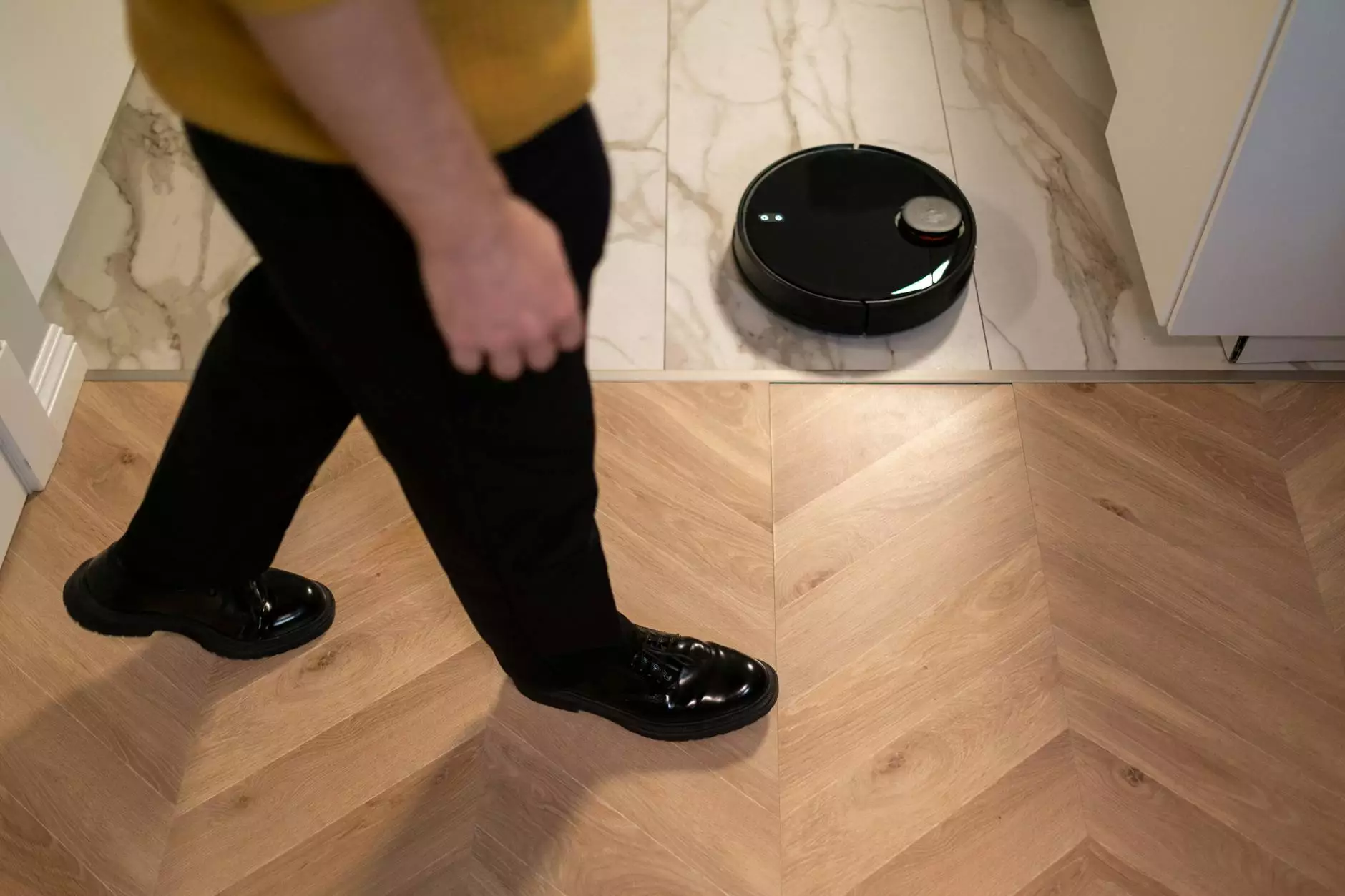
In the fast-evolving landscape of industrial technology, vacuum stations have emerged as critical components in numerous applications. These systems not only enhance productivity but also improve product quality in various sectors. This comprehensive guide will explore the significance of vacuum stations, their components, and tips for selecting the right vacuum system for your needs.
What is a Vacuum Station?
A vacuum station is defined as a setup that provides low-pressure environments, allowing for the manipulation of materials and processes without the interference of atmospheric pressure. These systems play a pivotal role in industries ranging from manufacturing and packaging to research and medical fields.
The Components of a Vacuum Station
Understanding the components of a vacuum station is vital for grasping its operational efficiency. Here are the main components:
- Vacuum Pumps: The heart of any vacuum station, responsible for creating and maintaining the vacuum atmosphere needed for various processes.
- Membranes: Silicone and natural rubber membranes are often used in vacuum applications due to their flexibility and resistance to deformation.
- Vacuum Chamber: A sealed enclosure where vacuum conditions are maintained, crucial for processes like drying, coating, or chemical reactions.
- Valves and Seals: Critical for maintaining vacuum integrity, preventing leaks and ensuring efficient operation of the system.
- Control Systems: These include sensors and software used to monitor and regulate vacuum levels for optimal performance.
Types of Membranes Used in Vacuum Stations
Among the many components found in a vacuum station, membranes play a significant role. The choice of membranes can greatly influence the performance and reliability of the system. Here are some common types:
1. Silicone Membranes
Silicone membranes are known for their high durability and temperature resistance. They are often used in applications requiring precise control of vacuum levels due to their excellent sealing capabilities.
2. Natural Rubber Membranes
Natural rubber membranes offer great elasticity and are suitable for various applications, especially in environments where flexibility is paramount. They are particularly helpful in processes that require consistent deformation without losing integrity.
3. Rubber Membranes
Various types of rubber membranes can be used, depending on the specific requirements of the application. Their resilience and ability to maintain shape under pressure make them a popular choice in many industries.
The Advantages of Using a Vacuum Station
The implementation of vacuum stations in industry brings various advantages. Here are some key benefits:
- Enhanced Product Quality: The ability to remove air and moisture from materials leads to higher quality finished products by minimizing defects.
- Increased Efficiency: Vacuum stations streamline processes, reducing the time needed for drying, curing, and other operations.
- Cost Savings: By improving yields and reducing waste, businesses can save significantly on materials and labor costs.
- Versatility: Suitable for a wide array of applications, from food packaging to chemical processing, vacuum stations can be adapted to meet specific needs.
- Improved Safety: By containing hazardous substances in a vacuum environment, safety is greatly enhanced during processing.
Choosing the Right Vacuum Station for Your Needs
For businesses considering the implementation of a vacuum station, understanding the factors involved in selection is critical. Here’s what to consider:
1. Determine Your Requirements
Assess the specific needs of your processes. Consider the materials you will be using, the desired vacuum level, and the scale of operation.
2. Evaluate the Types of Pumps
Different vacuum pumps serve various applications. Rotary vane pumps are common for standard applications, while turbo molecular pumps might be needed for high-precision tasks.
3. Consider the Size of the Vacuum Chamber
The size of the vacuum chamber should match your production needs. Larger chambers are suited for bulk processing, while smaller ones can be used for specialized tasks.
4. Assess Membrane Compatibility
Ensure that the membranes used are compatible with the chemicals and conditions they will face. This will extend the longevity of your vacuum station.
5. Factor in Maintenance and Support
Evaluate the maintenance needs of the vacuum station and the support offered by manufacturers or suppliers. Reliable support can save time and resources in the long run.
Applications of Vacuum Stations
Vacuum stations find extensive use across different industries, each leveraging the advantages that vacuum technology provides:
- Food Industry: Used in vacuum packaging to extend shelf life by removing air and preventing oxidation.
- Automotive: Employed in the manufacturing of components to prevent contamination and improve adhesion.
- Pharmaceuticals: Critical in processes such as freeze-drying and sterile packaging.
- Electronics: Essential in the production of components that require clean environments free from pollutants.
Conclusion
In summary, the role of vacuum stations in modern industry cannot be overstated. From enhancing product quality to providing significant operational efficiency, these systems have become indispensable across a multitude of sectors. By understanding the various components, advantages, and applications of vacuum stations, as well as how to choose the right one for your business needs, you can harness the full potential of vacuum technology. For more information and to explore a range of products, visit vacuum-presses.com, your trusted source for all things related to vacuum systems.