Understanding Phosphating Plants: A Crucial Component in Automotive Coating
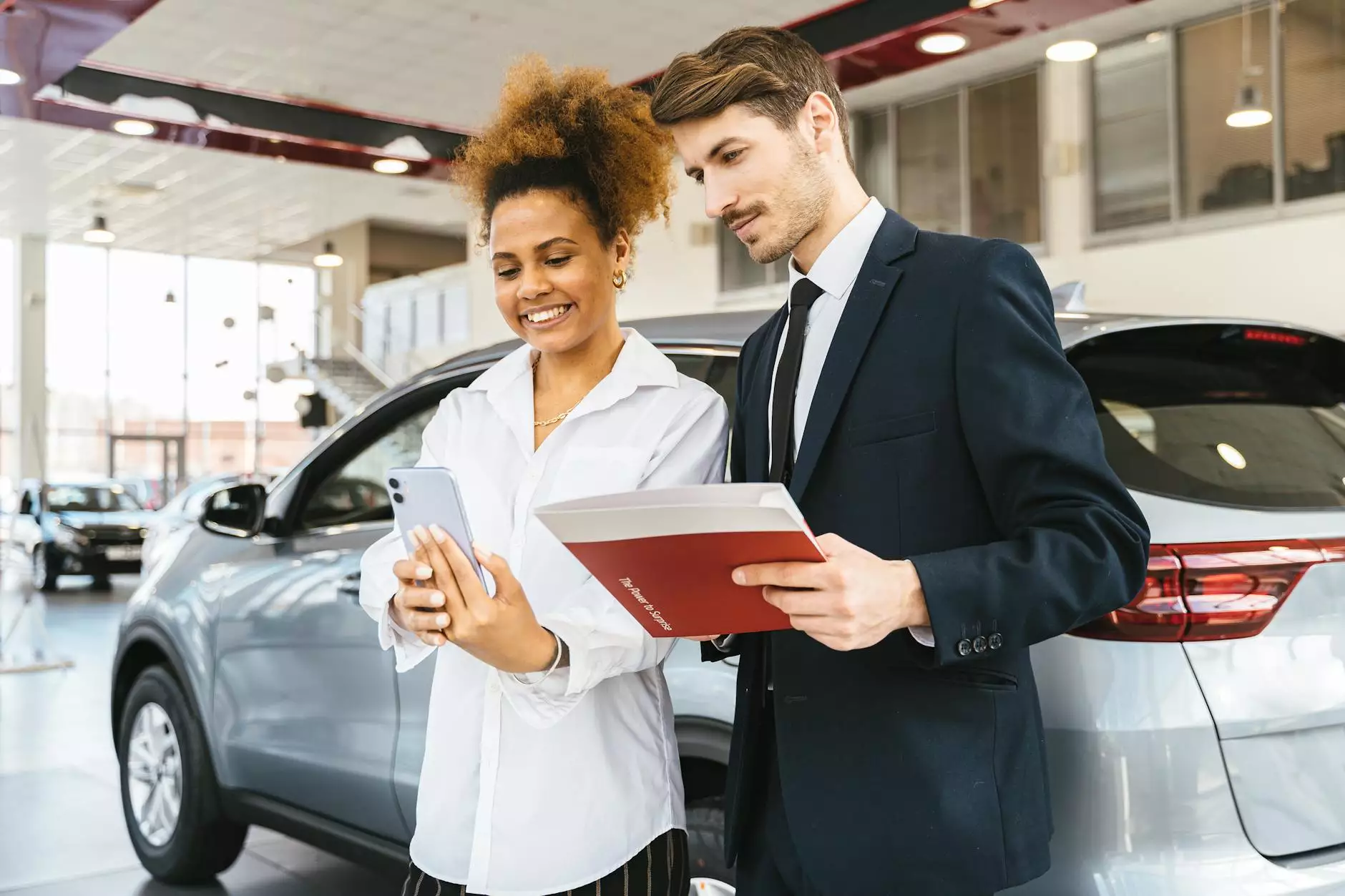
The phosphating plant is an essential part of the automotive manufacturing process, particularly in the context of surface treatment and coating. This article delves into the intricate details surrounding phosphating plants, exploring their importance, functionalities, and contributions to enhancing product performance in the automotive sector. We will also discuss the intersection of phosphating with the paint and sip industry, illustrating how these processes contribute to superior finishes and durability.
What is a Phosphating Plant?
A phosphating plant is a facility specifically designed for the application of phosphate coatings, a technique used to provide a corrosion-resistant layer on the surfaces of metals. This method is particularly crucial for automotive components, as it improves the adhesion of paints and other coatings while also enhancing the overall durability of the parts being treated. Such plants utilize various chemicals and processes to ensure that the coatings applied meet rigorous quality standards.
The Importance of Phosphating in the Automotive Industry
In the automotive sector, various components must withstand harsh environments and performance demands. The application of phosphate coatings serves several purposes:
- Corrosion Resistance: Phosphate coatings offer substantial protection against corrosion, extending the lifespan of automotive components.
- Adhesion Improvement: The presence of a phosphate layer significantly improves the adhesion of subsequent paint layers, ensuring better quality finishes.
- Lubrication Properties: Certain phosphate coatings provide lubrication, aiding in the assembly of parts and reducing wear during operation.
- Aesthetic Appeal: Phosphating enhances the appearance of components, contributing to the visual appeal of the final product.
Types of Phosphating Processes
There are several types of phosphating processes employed in the phosphating plant, each tailored to specific applications and product requirements. These include:
1. Zinc Phosphating
Zinc phosphating is one of the most common methods used in phosphating plants. It involves the application of a zinc phosphate layer that has excellent corrosion resistance properties. This type of phosphating is frequently used in automotive applications, providing a robust foundation for further painting and finishing processes.
2. Manganese Phosphating
This method utilizes manganese phosphate coatings, which are particularly useful for components subjected to high friction and wear. Manganese phosphate coatings are often found on engine parts, gears, and other critical components where durability is paramount.
3. Iron Phosphating
Iron phosphating is less common but still significant in certain applications. It provides a basic level of corrosion protection and is often used in less critical automotive components. This method is also utilized for pre-treatment processes before painting.
Phosphating Plant Equipment and Setup
Setting up a phosphating plant requires an understanding of the various equipment and systems involved in the process. Key components of these plants include:
- Pre-treatment Tanks: Before phosphating, parts must be cleaned to remove oils, rust, and dirt. Pre-treatment tanks house solutions that facilitate this cleaning process.
- Phosphating Tanks: These tanks contain the phosphating solution, where parts are dipped or sprayed to achieve the desired coating.
- Rinsing Stations: Rinsing stations are crucial for removing excess phosphating chemicals after the application process, ensuring the quality of the coating.
- Drying Chambers: After rinsing, components need to be dried to prevent any water spots or contamination before further processing.
- Quality Control Stations: These stations are vital for testing the thickness and quality of the phosphate coating, ensuring it meets the necessary standards.
The Phosphating Process: Step by Step
The phosphating plant operates through a series of well-defined steps, each critical to achieving a strong and effective phosphate coating. Here’s a breakdown of the common steps involved in the phosphating process:
1. Cleaning
The first step involves thoroughly cleaning the metal surfaces to eliminate contaminants that may interfere with the phosphate layer's adhesion. This can include degreasing agents and acid cleaners.
2. Rinsing
After cleaning, the components are rinsed in water to remove any leftover cleaning agents and contaminants, preparing them for the phosphating solution.
3. Phosphate Application
Components are then subjected to the phosphating solution, which may occur through immersion or spraying. The duration of exposure affects the thickness and quality of the coating.
4. Rinsing Again
A second rinsing phase occurs to wash away any unreacted phosphating solution and to halt the reaction process.
5. Drying
The components are dried using forced air or heating methods to ensure no moisture is left that could cause adverse effects in subsequent processes.
6. Quality Inspection
Finally, quality control tests are performed to ensure that the phosphate coating meets all specifications for thickness, adhesion, and appearance.
Innovations in Phosphating Technology
The manufacturing industry is constantly evolving, and phosphating plants are no exception. Numerous innovations in phosphating technology are emerging, including:
- Eco-friendly Solutions: New eco-friendly phosphating solutions are being developed that reduce harmful emissions and waste generation.
- Automated Systems: Automation in phosphating plants improves efficiency, reduces labor costs, and enhances consistency in coating applications.
- Advanced Control Systems: Implementing smart technology allows for better monitoring and control of the phosphating process, leading to higher quality outcomes.
Impact on Paint & Sip Industry
The phosphating plant plays a pivotal role not only in automotive manufacturing but also in the paint and sip industry. Understanding its impact involves recognizing how phosphating aligns with paint applications:
1. Enhanced Paint Adhesion
The improved adhesion provided by phosphate coatings supports the overall effectiveness of paint applications, ensuring that the paint remains intact even under challenging environmental conditions.
2. Surface Preparation
Before painting, the surface must be adequately prepared. Phosphating serves as an excellent primer, optimizing the substrate for painting.
3. Reducing Paint Defects
With better adhesion comes reduced potential for defects such as peeling or chipping, which are common problems faced in the paint and sip sector.
4. Extended Product Lifespan
Overall, the combination of phosphating with subsequent paint applications leads to longer-lasting finishes, essential for consumer satisfaction in the automotive industry.
Compliance and Environmental Considerations
With the increasing emphasis on sustainability, phosphating plants are also addressing compliance with environmental regulations. Key considerations include:
- Waste Management: Efficient waste disposal and management processes are necessary to prevent environmental contamination.
- Wastewater Treatment: Implementing advanced wastewater treatment systems helps in reusing water and minimizing ecological impact.
- Regulatory Compliance: Adhering to local and international regulations ensures that phosphating operations are sustainable and environmentally friendly.
Conclusion
In summary, the phosphating plant serves a crucial role in the automotive manufacturing and paint and sip industries, providing enhanced durability, corrosion resistance, and paint adhesion. As innovations continue to drive the industry forward, both the efficiency and sustainability of phosphating processes are set to improve. By acknowledging the importance of phosphating plants, manufacturers can ensure the production of high-quality automotive components that meet consumer expectations and regulatory standards.
For those in the automotive and related industries, understanding and leveraging the benefits of phosphating is essential for maintaining a competitive edge in today’s market.